Home > About Us > Services
Services
HYDRORESA, S.L. provides you with a complete service to guarantee optimum results in the cleaning and degreasing of metal parts or plastic parts, offering you access to all services connected with industrial washing and surface treatments from one single provider:
- Design and manufacture of BAUFOR industrial parts washers
- Technical service
- Supply of spares and parts
- Preventive maintenance programmes
- One-off maintenance sessions
- Adjustments and updates to industrial parts washers
- Restoration/rebuilds of old industrial parts washers
Design and manufacture of BAUFOR industrial parts washers
The design and manufacture of BAUFOR industrial parts washers for the spray washing and degreasing of parts has been our core business for more than 50 years now.
Our parts washers stand out as being turnkey projects, made to measure, which is why we work alongside our clients from the very outset, defining their specific needs and adapting the project to the parts to be washed/degreased.
At HYDRORESA, S.L. we believe that the only way to achieve optimum cleaning and degreasing results is to offer a customised solution. Feel free to contact us with no obligation.
Technical service
Our qualified technical staff are always on hand to resolve any problems or queries which may arise in connection with parts washers.
- We will often be able to resolve your problem over the telephone. A technical supervisor will analyse the event and propose the relevant solutions.
- If a telephone diagnosis is not possible, a technician will travel to your premises to evaluate the parts washer and its subsequent repair. If the problem requires the replacement or repair of parts or components, a price will then be quoted for the procedures required.
Supply of spares and parts
Our main aim is to guarantee our clients' satisfaction, which is why we offer a high-quality, swift and effective spares and parts supply service:
- Complete history of all components and parts for your BAUFOR industrial parts washer.
- Orders filled the same day they are placed.
- Shipment as promptly as possible.
- Urgent dispatch if required.
At HYDRORESA, S.L. we always recommend having the most typically employed spare parts in stock in order to avoid any unnecessary stoppages and downtime.
Preventive maintenance programmes
HYDRORESA, S.L. offers customised preventive maintenance programmes, the simplest way to protect your BAUFOR or other make of industrial parts washer through regular service inspections to guarantee optimum washing quality, prevent unexpected stoppages and higher repair costs.
Our maintenance programmes are scheduled on a customised basis in accordance with your specific needs and type of parts washer, make, characteristics and working conditions, and include:
- Evaluation of parts washer performance.
- Inspection of all components and report indicating those requiring repair or replacement.
- Spray nozzle cleaning and replacement if necessary.
- Calibration of pipelines and cleaning nozzles.
- Cleaning of chip baskets.
- General cleaning of the parts washer (chambers, tanks, etc.).
One-off maintenance sessions
Although HYDRORESA, S.L. recommends preventive maintenance programmes, we also offer a one-off maintenance service.
If for any reason you cannot plan sessions in advance they can be arranged on the fly whenever the client may feel the need. They include:
- Evaluation of parts washer performance.
- Inspection of all components and report indicating those requiring repair or replacement.
- Spray nozzle cleaning and replacement if necessary.
- Calibration of pipelines and cleaning nozzles.
- Cleaning of chip baskets.
- General cleaning of the parts washer (chambers, tanks, etc.).
Adjustments and updates to industrial parts washers
Adjustments and updates are the most cost-effective way of extending the service life of industrial parts washers or improving their performance for a lower cost than purchasing a new machine.
Our technicians will offer advice and suggest the required updates. Depending on the size of the update, the procedure may be performed on your own premises or at our workshops.
Some of the most common reasons for requesting an update:
- Receipt of new parts to be washed/degreased.
- Adaptation to new washing requirements.
- Incorporation of surface treatments within the process (descaling, phosphating, passivation).
- Increase in production capacity.
- Compliance with new regulations.
- Installation of a BAUFOR oil coalescer.
- Installation of filtering systems.
- Installation of protective or safety devices.
- Replacement of obsolete components (e.g. replacing float level indicators with inductive level detectors).
- Control panel update.
Restoration/rebuilds of old industrial parts washers
In many cases it is possible to restore old BAUFOR or third-party parts washers in order to obtain a machine which looks as good as new and offers the same performance as a new washer, for a lower investment cost.
As such projects take some time to perform, the restoration tasks would normally be carried out at our workshops.
A HYDRORESA, S.L. technician would travel to the client's premises to examine the current state of the parts washer. A report setting out the recommended actions would then be presented. The client decides which to implement, and as a result the investment required.
Some of the most common restoration procedures:
- Disassembly and inspection of all parts washer components, for repair or replacement.
- Cleaning of the parts washer outside and inside.
- Replacement of corroded or rusted parts.
- Repainting with epoxy paint, in the RAL colour chosen by the client.
- Fine-tuning.
- HYDRORESA, S.L.
- C/ Fogars de Tordera 65
- 08916 Badalona (Barcelona)
- +34 932 327 217
- +34 932 314 971
- baufor@baufor.com
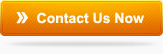